Jeśli chodzi o wysoki stosunek wytrzymałości do masy, to stopy tytanu są jednymi z najlepszych materiałów do produkcji ram rowerowych. Niestety, konstrukcje tworzone w tradycyjny sposób są dość drogie, ze względu na obróbkę. Dzięki technologii druku 3D można zmniejszyć ilość odpadów, a przez to cenę. Współpraca dwóch brytyjskich firm – Renishaw oraz Empire Cycles przyniosła owoc w postaci pierwszej na świecie wyczynowej ramy rowerowej ze stopu tytanu, wydrukowanej w 3D, która jest o 1/3 lżejsza niż tradycyjne, aluminiowe ramy.
Rama to podstawowa część roweru tworząca jego szkielet, do którego przymocowane są pozostałe elementy. Używane powszechnie ramy rowerowe zbudowane są najczęściej z rur ze stali, stopów aluminium, magnezu, tytanu lub kompozytów. Każdy z materiałów posiada swoje wady i zalety, dlatego w zależności od zastosowania kompozycje różnią się geometrią oraz składem chemicznym. Najstarszym materiałem do wyrobu ram rowerowych jest stal konstrukcyjna o podwyższonej zawartości węgla. Za stalą przemawia niska cena, łatwa obróbka, dostępność i szeroki wybór spośród różnej jakości stopów (różnią się głównie wagą i sztywnością). Tańsze produkcje są podatne na korozję oraz są stosunkowo ciężkie. Specjalnym typem jest nierdzewna stal chromowo-molibdenowa (Cr-Mo), która ze względu na domieszki posiada niewiele większy współczynnik wytrzymałości do masy od ram ze stopów aluminium (przy ponad dwukrotnie większej gęstości). Stal Cr-Mo posiada także doskonałą zdolność pochłaniania drgań.
Stopy aluminium to obecnie najpopularniejsza grupa materiałów do wytwarzania ram. Rury, które zdominowały rynek produkuje się ze stopów 6xxx (dodatek magnezu i krzemu) i 7xxx (dodatek cynku i magnezu). Ze względu na gorsze właściwości mechaniczne, średnice rur mają większy przekrój niż ich stalowe odpowiedniki (przy gęstości 2,7-2,8 g/cm^3) . Cechuje je duża sztywność, przez co tłumienie drgań jest słabsze. Takie ramy pokrywane są naturalnie przez cienką warstwą tlenku aluminium, co wpływa na zwiększenie ich odporności korozyjnej.
Ramy z materiałów kompozytowych zbudowane są zazwyczaj z włókien węglowych i/lub aramidowych formowanych w postaci tkanin. Łączy się je za pomocą żywic poliestrowych i epoksydowych, dzięki czemu rama może przyjmować dowolny kształt. Własności mechaniczne zależą m.in. od rodzaju włókien i żywic, liczby i kąta ułożenia warstw. Posiadają bardzo dobre własności amortyzacyjne, są całkowicie odporne na korozję oraz bardzo lekkie (nawet około 0,6 kg). Wadą takich konstrukcji jest mała odporność na gięcie boczne, a w razie uszkodzenia praktycznie brak jest możliwości ich naprawy. W kolarstwie górskim polegającym na dynamicznym zjeździe i skokach, ramy z włókien póki co nie spełniają narzuconych wymagań.
Skoro istnieje tak wiele alternatyw, dlaczego tytan jest tak bardzo pożądanym materiałem? Zakup roweru z tytanu to inwestycja na całe życie. Taka rama jest praktycznie nie do zdarcia. Stopy tytanu gwarantują wysoki stosunek wytrzymałości do masy. W połączeniu z bardzo dobrą odpornością na korozję (podobnie jak w przypadku glinu, tytan w kontakcie z tlenem pokrywa się dodatkową warstwą ochronną tlenku TiO2), wytrzymałością stali i ponad 60% niższą masą, znakomitym tłumieniem drgań, metal wydaje się być idealnym surowcem na ramy rowerowe. Niestety, ciągle jest to rzadko stosowany materiał, na który nie stać każdego. Luksusowe, tytanowe rowery są tak drogie nie tylko ze względu na koszty jego wytworzenia, ale także z powodu trudnej obróbki. Czysty tytan nie nadaje się do produkcji rur, gdyż zbyt łatwo ulega odkształceniom pod wpływem obciążenia. Stop z dodatkami aluminium i wanadu (np. Ti3Al2,5V) posiada już odpowiednie cechy: gęstość 4.48 g/cm^3, wytrzymałość na rozciąganie od 621 do 740 MPa, umowną granicę plastyczności (0.2% odkształcenia trwałego) od 483 do 607 MPa, moduł Younga 91 GPa, twardość Rockwella w skali C równą 15 HRC oraz dobrą spawalność [4].
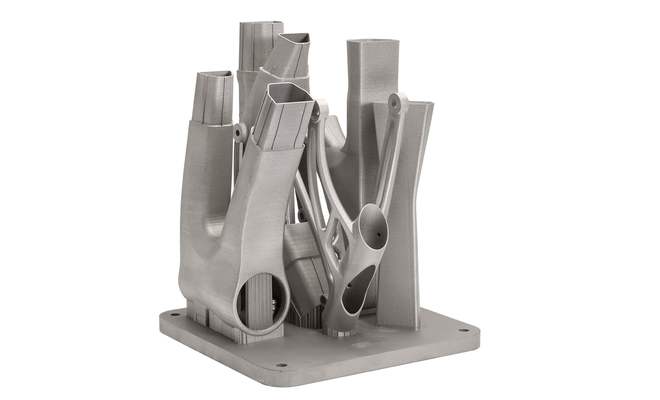
Tak wyglądają tytanowe elementy ramy wydrukowane w procesie laserowego spiekania proszku. Materiały prasowe – Copyright Renishaw.
Plastyczność materiału, bardzo duża wytrzymałość mechaniczna i twardość sprawiają, że do obróbki skrawaniem trzeba stosować specjalistyczne, drogie narzędzia, które pozostawiają odpady. Ze względy na reaktywność z tlenem, elementy tytanowe spawane są w osłonie gazów obojętnych (np. argonie), co znacznie podnosi koszty produkcji. Redukcję wydatków może zapewnić technika druku 3D. Jest ona korzystna finansowo, gdyż umożliwia zmniejszenie ilości skrawków materiału, w porównaniu do tradycyjnych metod produkcji i obróbki elementów metalowych.
Renishaw i Imperium Cycles zbudowały ramę ze stopu tytanu do roweru górskiego MX-6 Evo Mountain, którego szkielet do do tej pory był wykonywany ze stopu aluminium. Do wytworzenia elementów wykorzystali drukarkę laserową AM250 umożliwiającą laserowe spiekanie proszków. Komora spiekowa posiadała wymiary 250 x 250 x 300 mm (X, Y, Z) z możliwością przedłużenia osi Z do 360 mm. Drukarka zapewniała możliwość wytworzenia wysokiej jakości, jednolitych części o porowatości niższej niż 0,3%. Spiekanie odbywało się w atmosferze argonu, co miało znaczenie przy tworzeniu członów z materiału reaktywnego. Przed wykonaniem modelu rzeczywistego, zoptymalizowano geometrię tytanowej ramy poprzez symulacje komputerowe. Projekt został wykonany w taki sposób, aby w pełni wykorzystać rozmiary komory roboczej. Określono także, gdzie można zredukować przekrój bez wpływu na wytrzymałość konstrukcji. W rezultacie otrzymano produkt o masie 1,400 g, czyli o 33% mniej niż ważył aluminiowy poprzednik (2,100 g). Wytrzymałość sztycy (wspornika siodełka), z sześciokrotnym zapasem spełniała normę bezpieczeństwa dla rowerów górskich EN 14766. Poszczególne elementy posiadały odpowiednie miejsca łączenia, ułatwiające spajanie klejem.
Spiekanie laserowe ma swoje zalety, gdyż niewykorzystany proszek można użyć do budowy następnych elementów. Zmiana geometrii nie sprawia problemu, tak jak w przypadku części produkowanych metodą odlewania (konieczność stworzenia nowej formy). Ułatwione jest także tworzenie skomplikowanych członów. Pozostaje tylko czekać na upowszechnienie technologii i zainteresowanie ze strony innych producentów.
Spiekanie laserowe – drukowanie 3D na maszynie Renishaws AM250.
Źródło:
[1] http://www.renishaw.com/en/first-metal-3d-printed-bicycle-frame-manufactured-by-renishaw-for-empire-cycles–24154 [12.02.2014]
[2] http://www.geeky-gadgets.com/worlds-first-titanium-alloy-3d-printed-bike-frame-10-02-2014/ [12.02.2014]
[3] http://www.gizmag.com/3d-printed-titanium-bicycle-frame/30760/ [12.02.2014]
[4] http://www.azom.com/article.aspx?ArticleID=1728 [12.02.2014]
[5] http://www.renishaw.com/en/am250-laser-melting-machine–15253 [12.02.2014]
[6] Bike Arc Modular Bike Park System by Richard Masoner, flickr.com, CC BY-SA 2.0